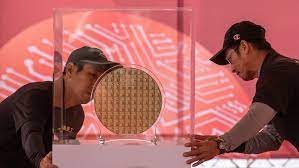
Geopolitical risks are driving efforts to diversify but there are no quick solutions
It is a year since New York Federal Reserve economists unveiled the Global Supply Chain Pressure Index. The barometer of port backlogs and freight costs, looking back over 25 years, showed that constraints on moving goods around the globe peaked in late 2021, at a level for which they could find no precedent.
The gauge started to fall as economies slowed, and as Covid-19 disruptions eased. Then Russia invaded Ukraine. As governments and multinationals scrambled to navigate the fallout, the index eased back, only for progress to be stalled by an upsurge in Covid-19 cases in China as 2022 ended.
Michael Farlekas, chief executive of freight-booking software company E2open, likens his client’s response to the stages of grief: “At first you’re shocked, then at some point you reach acceptance.”
Present high inflation, rising interest rates, and geopolitical tensions add up to “an urgent imperative for a robust supply-chain response if operations are going to remain profitable, or even sustainable”, McKinsey management consultants warned recently.
Among the risks consultancies and credit rating agencies foresee are an energy crisis in Europe which could idle industrial exporters; relations between China and the west deteriorating such that Beijing blocks rare earth exports; and a China-Taiwan conflict, which could devastate a vital source of semiconductors.
Regarding the last of these, the fear of a drastic interruption in the supply of electronic chips — the Asian Development Bank estimates that 65 percent of all goods exports depend on them, and Taiwan is the world’s biggest producer — has become an overriding preoccupation.
Regarding the last of these, the US, China, the EU, Japan, and India have promised a total of $190bn in subsidies to build domestic semiconductor manufacturing industries, New Street Research estimates.
Companies, too, are looking for sources closer to home, with US technology company Dell telling suppliers it wants to phase out made-in-China chips by 2024, Nikkei Asia reports.
As companies re-examine supply chains designed for low costs rather than to withstand extreme disruptions, the terms “reshoring” and “friendshoring” — sourcing from allied countries — have become boardroom buzzwords.
“It is not the CEO’s job to be political. It’s the CEO’s job to make sure the customers have their product,” says Tim Ryan, US chair of professional services firm PwC. Covid taught business leaders to avoid concentration of supply lines, Ryan adds. Executives are now trying to diversify but “most companies can’t change a supply chain overnight”.
The most common workaround is dual sourcing, says Marshall Fisher, a professor at the Wharton School of the University of Pennsylvania, as “being dependent on a single supplier anywhere has a lot of risks”.
Executives are saying, “I just have to take control of my own fate,” echoes Farlekas, and trying to find savings elsewhere to offset the higher costs of a diversification strategy often referred to as “China plus one”. But, as inflation and slowing demand weigh on corporate profits, will cost considerations slow this drive for resilience?
Ryan thinks not, observing that production costs were once the dominant factor in companies’ sourcing. Executives now use “a broader lens”, looking at factors including climate risks, which have pushed clients to review suppliers located in areas prone to flooding or drought.
Even so, Ryan sees the most activity is where such climate effects are already affecting businesses, as it is easier for boards to justify long-term spending if they are already bearing the costs of extreme weather.
Other sustainability questions are preoccupying businesses and governments. Electric carmakers, including Tesla, have been pressing for better supply chain traceability to root out cobalt linked to child labor in the Democratic Republic of Congo.
Chile has agreed to Brussels’ demands on environmental protection and human rights to update an EU trade deal covering lithium and copper supplies.
Globalized supply chain complexities are driving support for the cause of bringing more production home, or to friendly neighbors.
Fisher cites, however, a vivid image of supply shortages from the start of the pandemic. Empty shelves where the toilet paper should have been on sale belied the fact that most US toilet paper is made in North America.
“One factory in Pennsylvania, where I live, is just 10 miles from the store where I was experiencing stock-outs,” Fisher recalls. “Friendshoring is not a panacea.”